Fairbanks Welding Class
A HUGE shutout to Adam Porter and Roy Rich in Fairbanks, hosting a the fourth TIG Class. Along with Eric who provided fantastic welding theory and advice for the whole class. With everything great that comes with the classes we don’t plan on stopping them! Reach out to the Fairbanks Team for more information
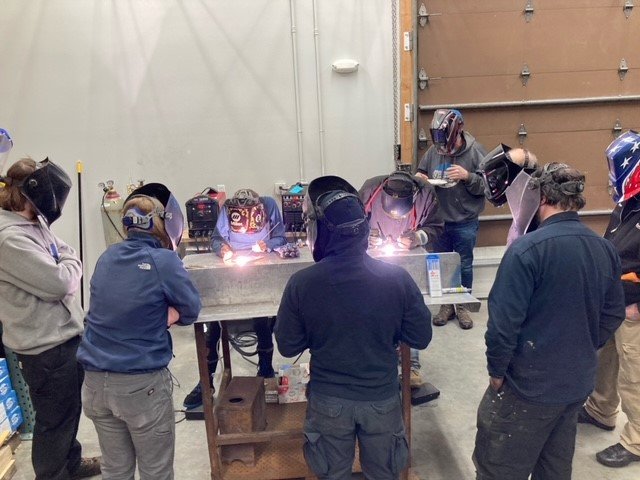
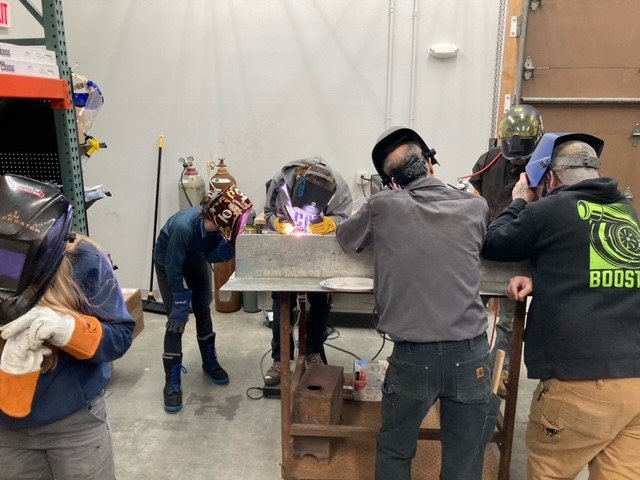
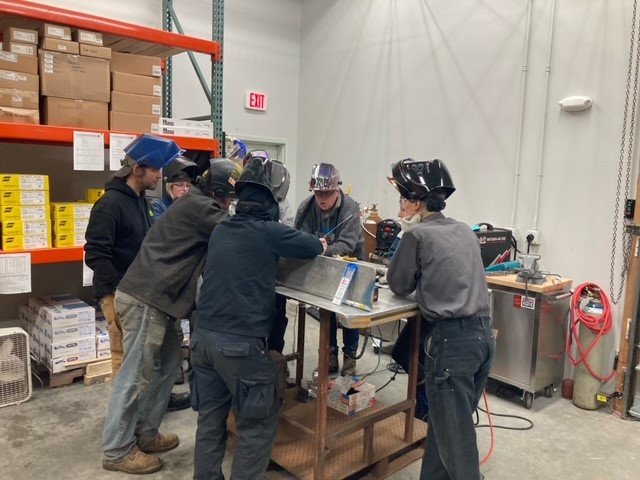
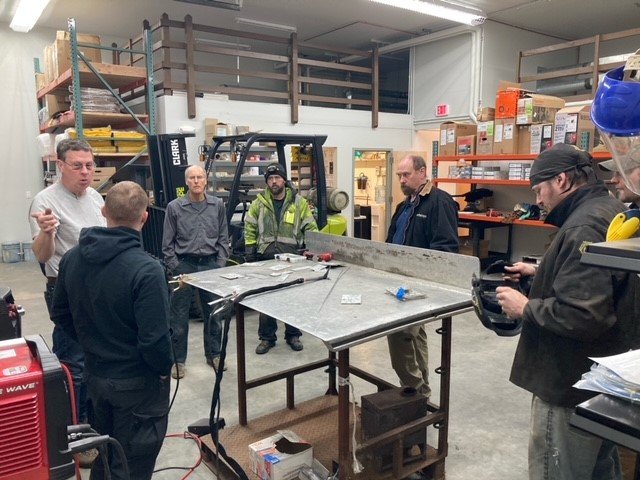
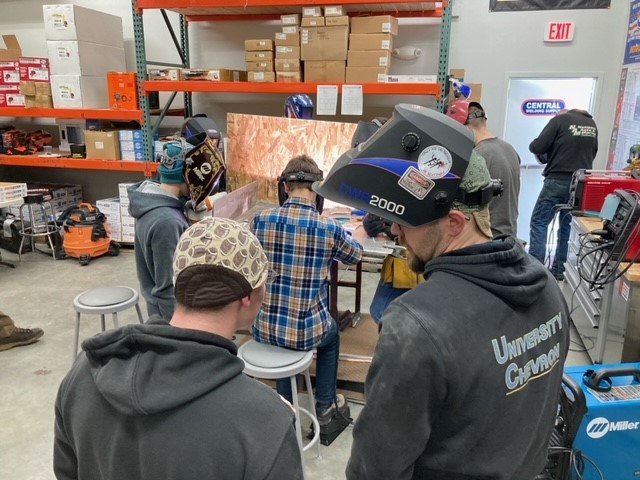
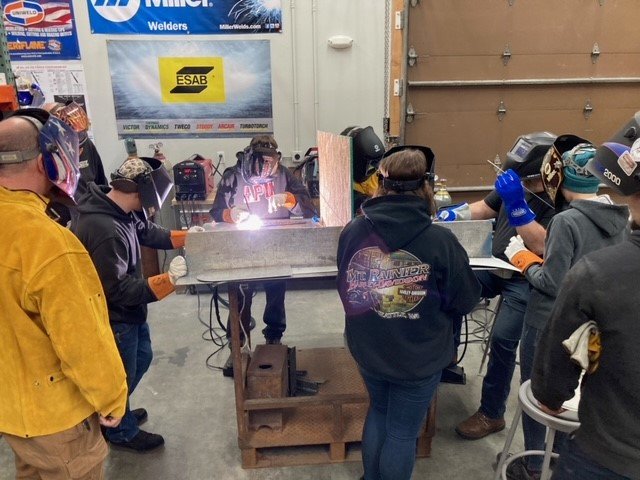
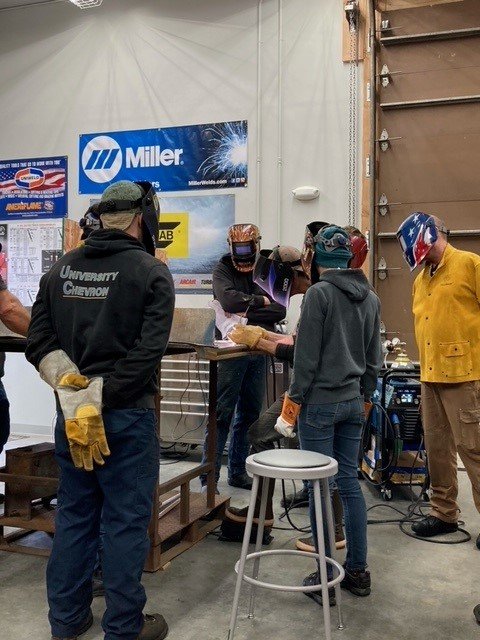
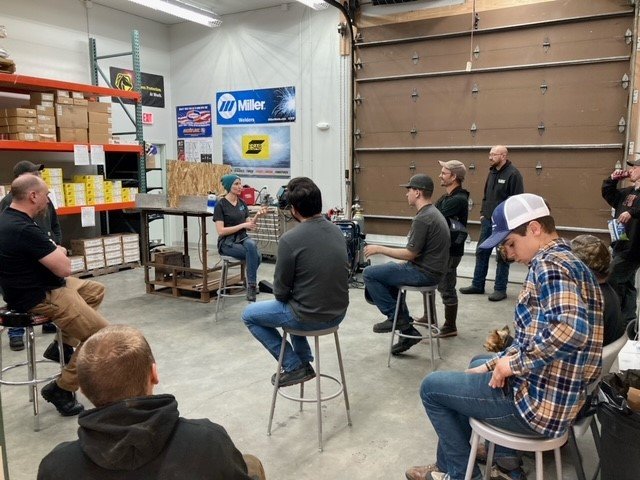
6 Tips For Getting Better Quality TIG Welds
One of the biggest advantages of tungsten inert gas welding, or TIG welding (gas-tungsten arc welding GTAW), is that you can use it to weld both ferrous and non-ferrous metals. It also offers the highest quality welds, excellent bead appearance and is more versatile; allowing you to weld thin and thick metal, while fully controlling the arc.
On the other hand, it is the lowest deposition process and requires more set-up time than some other processes and requires more welder skill than other wire-fed processes. Besides proper prepping, here are some other do’s and don’ts for getting better-quality TIG welds.
#1: Put on PPE.
You’re not going to get a lot of sparks with TIG, but the proper protective gear is still important. This includes leather gloves, a helmet, a long flame-resistant shirt, and, if you’re working in an enclosed area, a respirator or clean air system.
#2: Set Up Properly.
For aluminum welding, switch your polarity on the front panel to AC or DCEN. For steel, and other metals, switch your polarity setting to DCEN. Choose the correct tungsten and prepare the tip properly for the polarity and base material you are welding. Also, when grinding your tungsten, make sure you grind parallel with the length of the electrode to promote better arc stability.
#3: Push the Torch to Get a Good Bead.
To get a good bead, push the torch, forming the bead puddle on the material, while keeping the tungsten out of the puddle, and then dip your filler rod, if using, into the molten puddle as you weld.
#4: Don’t Let Your Arc Get Too Long
Don’t let your arc length get too long, melting the filler before it gets into the puddle. This leads to a poor-quality welds and potentially lack of fusion at the root of the weld.
#5: Don’t Dip Your Tungsten
Keep your tungsten 1/8th to 1/16th of an inch away from the weld puddle. This will ensure a stable arc and prevent tungsten contamination in your weld bead.
#6: Don’t Feed Your Filler Rod Too Far
As you’re welding, all the heat is coming off the tungsten. Feeding the filler rod from too far away from the weld joint may cause the filler to contaminate the tungsten and the arc will become less focused and unstable.